http://api.ning.com/files/HAVVJu2zjUSpk ... Vinson.pdf
Some of you have seen this, I'm sure, and opinions vary from "It's the best idea ever conceived" to "total waste of time", depending who you listen to, typical for amateur Luthiery, I find. I had most of the hardware and lumber kicking around. Including buying some inserts, threaded rod, and a second dial indicator, I'm into it for around $36, not too bad if its wasted, I guess. I had to re-lvel the fingerboard on a build in progress, neck through design, and the half-built jig served quite well for that purpose:
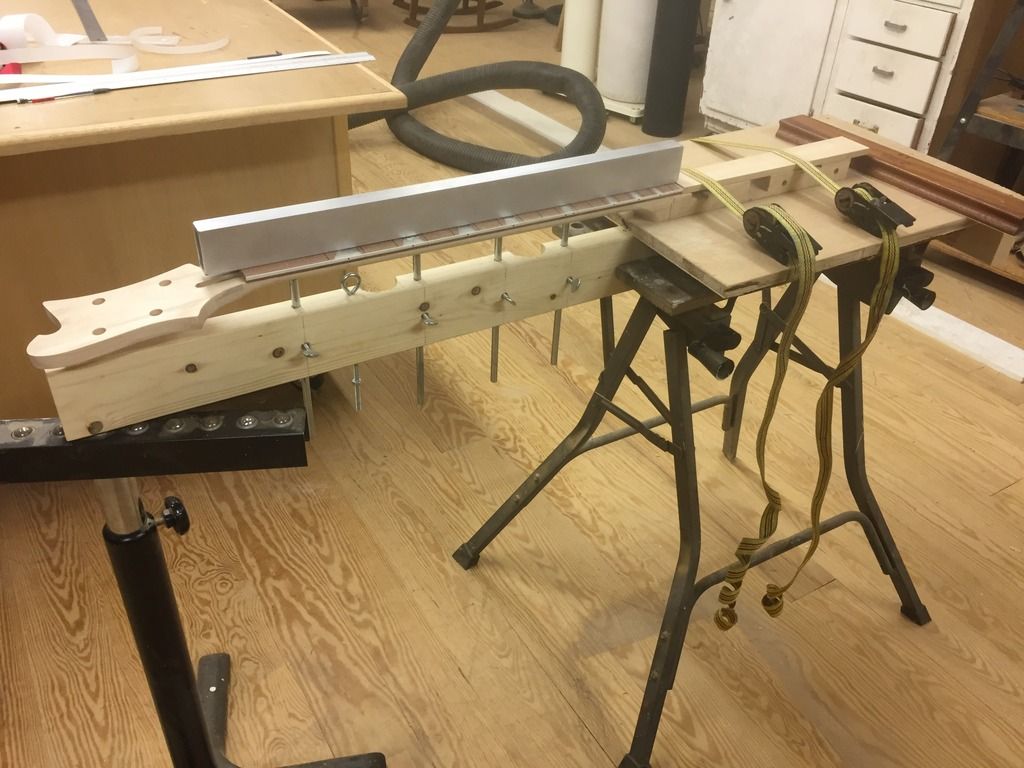
I realized the 2x4 pine main beam isn't stiff enough in this cantilvered configuration, going to add some scrap angle or a bed rail to stiffen it up, and maybe add a vertical "leg" with a leveling foot. This has yet to have a headstock jack or dial indicators installed.
I understand the basic concept of re-creating the neck conditions under string tension and adding the effects of gravity by tilting up to playing position, but I have a fundamental question:
All the examples of either this or the actual Stewmac jig in use show the operator using a fret slotted straightedge to get the FINGERBOARD dead flat with trussrod adjustments prior to setting the dial indicators to zero, and then re-creating this zero with the strings removed prior to fret leveling by adjusting the headstock jack and nut pulldown strap. No mention of any fingerboard relief ever comes up. I dont understand how this can be discounted, since a perfectly flat neck is effectively unplayable, as I understand it. Any clarity on procedure for fret leveling with this or similar jigs greatly appreciated.